Powell River Project - Stabilizing Reclaimed Mines to Support Buildings and Development
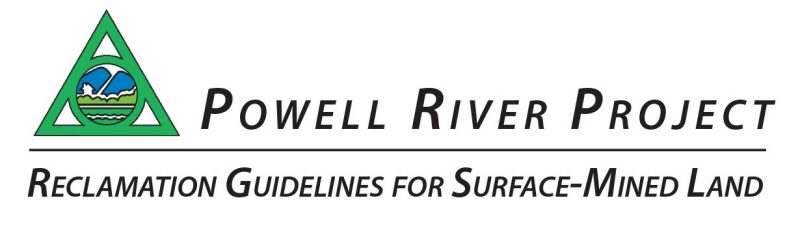
ID
460-130 (CSES-214P)
EXPERT REVIEWED
Introduction
Land-use constraints hinder economic activity in the Virginia coalfield region; the lack of flat land hinders infrastructure construction, industrial recruitment, and business development. Reclaimed coal mines are widely discussed as potential development sites, but modern reclamation rarely prepares mined areas for building-support purposes. This publication describes mine-stabilization procedures that can be employed for developing reclaimed mine areas for building construction.
This publication outlines general concepts and guidelines. Parties seeking to construct buildings on any mined area should engage the services of a professional engineer.
Background: Land Settlement and Structural Distortion
A critical factor affecting suitability of reclaimed mines for building construction is surface stability. As filled lands, virtually all reclaimed mines will be subject to some settlement, or consolidation, over time. Although it can damage utility connections, a uniform, even ground settlement of 2 inches or less will generally cause little or no damage to most building types.
“Differential settlement” – where the depth of settlement varies under different parts of a structure – can damage buildings through “structural distortion.”
Differential settlement is common on reclaimed mines, and it occurs when significant variations in depth, composition, or compaction are present in spoils underlying a building site.
The factors affecting settlement of reclaimed mine lands and building structures’ tolerance to settlement are reviewed in Foundations for Housing on Reclaimed Mined Lands, Virginia Cooperative Extension publication 460-115. Rigid or semirigid structures employing large volumes of concrete and structures covering large lateral areas are particularly sensitive to distortion and damage due to differential settlement.
It is especially important to construct land that will minimize differential settlement if an industrial use is intended for a reclaimed site. Industrial facilities typically employ concrete floors covering large areas. High-value manufacturing and processing operations typically require high levels of mechanical precision; a shifting or cracking concrete floor will not be compatible with such activities. Nonreinforced masonry structures will be especially sensitive to settlement.
Mine Reclamation Procedures to Minimize Differential Settlement
Reclaimed mines are best able to accommodate building construction when building locations are identified prior to mining so that reclamation procedures can be designed to produce a stabilized building site.
Spoil Depth
Buildings should be located in areas where spoil depth is relatively uniform. Ideally, buildings will also be placed in areas where underlying spoil depth is relatively shallow. In a conventional contour-mining operation, building sites should be located over solid bench areas – not hollow fills.
Maintaining a uniform spoil depth under building locations helps to avoid differential settlement (see figure 1). All spoils will settle, regardless of placement procedures; the depth of spoil will be a major factor that influences the amount of settlement. If spoil depths under a building site are even and uniform, ground settlement is more likely to be even and uniform. Locating a building site where spoils are of minimum practical depth will reduce the costs of spoil-placement and site-stabilization procedures, if employed.

If only a portion of the reclaimed site will consist of shallow spoil over a solid bench area, it is important to survey prior to spoil placement so the area suitable for building construction can be precisely located after mining and reclamation are complete.
Spoil Placement
Spoils underlying areas being prepared for building construction should be placed in a controlled fashion.
The spoil-placement procedures recommended below would be more costly than those typically employed by Appalachian coal surface mines; they are intended to minimize settlement-induced distortion of overlying building structures.
The following are factors that should be considered when developing a mine-reclamation plan for a site intended to support a high-value building:
1. A building-support “pad” should be constructed using controlled spoil-placement procedures.
A well-defined spoil pad should be carefully constructed under the planned location of the building and its immediate surroundings using controlled-placement procedures (see figure 2). The pad should extend beyond the building’s perimeter by at least 10 feet in all directions. General guidelines for construction of the spoil pad follow, but a professional engineer with access to accurate data describing material properties and settlement characteristics of available mine spoils should design the procedures. At the conclusion of pad construction, the area should be surveyed so the pad’s exact location can be identified after reclamation is complete.

2. The building-support pad should be constructed through placement of spoil in lifts of controlled thickness.
The ideal thickness of each lift will depend upon a variety of factors, including physical factors such as the spoil’s engineering characteristics and the type of equipment available for spoil compaction. Other factors will include the total depth of spoils that will underlie the building, the length of time likely to elapse between spoil placement and building construction, and the building’s design.
A lift thickness of about 1 to 2 feet will be sufficient to minimize settlement in most situations if that lift is thoroughly compacted. Achieving this 1- to 2-foot lift thickness will not be economically feasible on most mines. A 2- to 4-foot thickness, although not ideal, will achieve a reasonable level of stability if compacted uniformly and if spoil composition is controlled. Mine spoils with a composition dominated by hard sandstone spoils and rock fragments will compact more effectively at 3- to 4-foot thicknesses than spoils with composition dominated by shale and clay. If operational problems prevent spoil placement in lifts that are 4 feet or less in thickness, use of controlled lifts of minimum practical thickness (even if thicker than 4 feet) with controlled composition would be a superior practice to random dumping.
3. The composition of spoils in each lift of the building-support pad should be carefully controlled.
Ideally, spoils within each lift should be of a single rock type, although this may not be practical at some sites. If possible, use of rock fragments larger than 1 foot in diameter should be avoided during construction of the building-support pad. Use of a hard, competent material (such as durable-rock sandstone) is preferred to use of rocks that will slake in water, such as most siltstone and shale.
From a purely geotechnical standpoint, the best procedure to minimize settlement would be to utilize a screening procedure so as to rigorously control rock fragment size while building the support pad.
An alternative practice – one that is not ideal from a geotechnical standpoint but is less costly – would be to control the spoil fragment size, as well as the rock type, of the building-support pad by exercising control over spoil-movement procedures. Under this practice, spoil excavation and movement procedures would employ one or more alternate dumpsites that do not underlie future building areas. If the spoil is being moved by truck, the truck operator can be instructed to dump loads containing materials that are not suitable for building support in an alternate dumpsite location, while suitable materials are placed in the building-support fill.
The loader operator will be the person on most jobsites who has the best view of the material in each truckload. The loader operator can be instructed to direct spoil movement by communicating with the truck operators. Given a small number of dumpsite locations, hand signals (viewed by the truck operator through the rearview mirror), horn signals, or other means of communication can be used by the loader operator to direct spoil movement.
If mining economics prevent placement of material in compacted lifts of controlled thickness, the stability of the postmining landform will be increased if the composition of spoils placed in areas of potential building construction is controlled. Use of hard sandstone spoils and exclusion of siltstone and shale in areas of potential building construction will enhance the postmining stability of those areas, even if spoil is not placed in compacted lifts. If this practice is followed, it will be important to document the location of those lands constructed using hard sandstone spoils through a survey or other means.
4. Each lift should be thoroughly compacted in place.
Special compaction equipment, such as a vibratory roller, can be employed to achieve a thorough and uniform compaction of each lift. Such practice is preferred from a geotechnical standpoint. However, use of specialized compaction equipment will be cost-prohibitive for most coal-mining operations.
An alternative method of achieving spoil compaction will be to use loaded haul trucks. As loaded trucks drive over previously placed spoil to reach the dumpsite, significant compaction will occur (see figure 3). The challenge to the mine supervisor will be to design a spoil-placement sequence that will cause compaction to occur as a result of routine spoil movement. Truck drivers can be instructed to vary the location of each route so as to achieve more-or-less-uniform wheel coverage over the entire compaction area. If this procedure is employed, it will be important to maintain consistent lift thicknesses. Generally, the weight of a track dozer will not be sufficient to compact spoil to the degree necessary to achieve a stabilized building support.
Mine spoils cannot be compacted effectively if they are extremely dry or extremely wet. If a high-value building is to be constructed on the reclaimed site and the goal is to reduce postreclamation settlement to an absolute minimum, spoil placement procedures should be designed with an engineer’s input so as to assure spoil-moisture contents that are optimal for compaction. The optimum moisture content for compaction of most mine spoils containing large quantities of soil-sized materials will range from 5 percent to 15 percent.

On most operating surface mines, use of procedures to exert firm control over spoil moisture content during compaction will be cost-prohibitive. On eastern U.S. mines, spoils in the field will rarely become too dry for effective compaction; however, they can become too wet during damp weather. The effect of compaction is to press the mineral particles close together, reducing pore volumes and the opportunity for further consolidation. When spoils are extremely moist, water occupying the pores between small mineral particles effectively limits the ability of the particles to be forced together. Therefore, it is advisable to avoid placement and compaction of building-support pads during wet weather whenever possible.
5. The building-site fill should be well-drained.
A buildup of water in the fill can cause substantial settlement – even if it occurs many years after fill placement. Surface drainage, building placement, the orientation and pitch of subsurface compaction planes, and the placement of rock underdrains are factors that can help to prevent a buildup of water in the fill. For example, construction of a building-support pad using lifts that have slight crowns would be a superior practice to construction of lift surfaces that drain inward. Large, durable rock fragments can be placed at the base of those spoils that surround the building-support pads so as to assure adequate drainage.
Summary
The above procedures can minimize postreclamation settlement – but they will not eliminate it. Settlement differentials of 1 inch or more can have a substantial damaging effect on most building types.
When land is constructed using the above procedures, precautions remain in order. After mine-fill construction is complete, some time should be allowed to pass prior to building construction. Survey points should be established to monitor postmining settlement; only when settlement has slowed to acceptable levels should construction begin. Settlement will be most severe during the first year following spoil placement.
Thorough documentation of procedures employed to construct the building-support pad will aid future building and site design. Periodic visits of a geotechnical engineer to the site during construction will be the best way to provide that documentation. If the engineer who designs postmining site usage does not have precise knowledge of the procedures used to construct the reclaimed landform, the resulting building/site design is likely to be more conservative (and more costly) than necessary. If the engineer is able to come onto the site periodically to observe controlled spoil-placement procedures and obtain spoil samples, site-usage design can accommodate those spoil-placement procedures that did occur.
Building on Sites Prepared Using Conventional Spoil Placement
In Appalachia, common land-reclamation procedures do not make extensive use of controlled spoil-placement procedures such as those described above. Nonetheless, there will be opportunities to develop reclaimed mines, even when the reclamation has not used optimal procedures.
Several options are available for building on settlementprone, reclaimed mines. These are described below.
Option 1: Allow the Site to Stabilize
Eventually, the passage of time will stabilize virtually all reclaimed-mine sites. In some cases, construction of small buildings has been successful on older mine sites once enough time has passed to allow the rate settlement to slow. In most cases, larger buildings on spoils of significant depth that have not been compacted in place will require site-stabilization procedures.
Figure 4 represents depth of settlement with time in minespoil fills of various characteristics. Depth of settlement after the first year was calculated using the formula:
TS = A*H*(LogT1-LogT2)/100
where TS represents total settlement, H represents the fill height, and T1 and T2 represent time after mining expressed in years (Krebs 1987). A is a settlement factor that varies with spoil composition. Figure 4 was constructed using a settlement factor of 1.0 for loose siltstone and 0.2 for compacted sandstone. The sandstone settlement factor represents excellent compaction of material placed in 1- to 2-foot lifts. Figure 4 shows that a 100-foot depth of loose siltstone spoil would be likely to settle about 1 foot between the second and 10th years after mining, and another foot in the 90 years after that. The compacted sandstone fill would settle about one-fifth of these amounts.
These figures represent settlement of nonsaturated spoils. If spoils become saturated due to a high water table or a concentration of surface water on the site, more rapid settlement can be expected during and immediately following saturation.
While Figure 4 represents total settlement, differential settlement is what damages buildings. If the spoil in the building-support fill is relatively uniform in physical characteristics and degree of compaction, settlement differentials are likely to be only a fraction of the total settlement represented in Figure 4.
If an expensive building design is to be employed, placing survey stakes and measuring actual settlement through at least one winter season prior to building would be desirable.

If settlement of the mine-fill surface is continuing, removal of surface spoils to the depth of a design surcharge (see option 4) will expose spoils that have been stabilized by the weight of overlying materials and may be suitable for building, depending on the nature of the underlying material and the age of the fill.
Option 2: Use a Building Design That Can Tolerate Settlement
This can be an option for some structures, depending on the owner’s intended use for the site. One strategy would be to employ a building design that could accommodate distortion without losing functionality. Manufactured housing is typically able to withstand distortion due to settlement better than site-built homes because of design features intended to help the building withstand the rigors of transportation. Small, portable buildings such as trailers can be built with accessible support points that will enable adjustment of supporting piers through shimming or other means – if such an adjustment becomes necessary as a response to differential settlement. Metal-shell buildings can typically tolerate higher levels of distortion than many other building types.
Another strategy would be to use a rigid structure that is capable of withstanding the settlement of underlying ground. For relatively small buildings, a prestressed concrete slab can be designed to “float” on the mine-spoil surface, bridging whatever voids may develop and remaining rigid despite any differential settlement of underlying materials. Larger buildings can also make use of prestressed slabs, but with greater design difficulty and expense. Nonreinforced masonry is poor in ability to withstand differential settlement without fracturing. Concrete block is generally a poor choice for a construction material on settlement-prone ground.
Option 3: Install Piers to Support Building on Stable Ground
A third possible strategy would be to set piers or pilings through the mine spoil. If the piers are strong enough to support the building and long enough to reach undisturbed ground, they should provide a stable support despite any settling of the mine spoils that underlie the building. Generally speaking, drilling piling locations will be preferable to driving the pilings, especially in a stony mine spoil. Pilings are an expensive way to support buildings on all but the thinnest mine spoils, where it may make greater economic sense to excavate and replace underlying spoil than to place the building on pilings.
Option 4: Employ Procedures to Stabilize the Building Site
In cases where a stable building support must be assured, it is possible to treat the spoil that has been placed on the mining site in a manner that will increase the ground’s stability as underlying support for the building structure. Any one of several methods may be used to achieve this goal.
Depending on spoil thickness, it may be possible to excavate spoil from beneath the building’s location; the spoil could then be replaced using controlled-placement and compaction procedures.
Another option would be to compact the inground spoil using mechanical methods. Several procedures are available to achieve this goal. A procedure called “dynamic compaction” employs a heavy weight that is dropped from a specified height in a repetitive grid-like pattern to compact the uppermost spoil layer. When prescribed, dynamic compaction is typically intended to achieve a tightly compacted “zone” of spoil constituting the upper 15 to 30 feet of the fill. This tightly compacted zone is expected to remain rigid despite any settling of the underlying noncompacted spoil, thus acting in a fashion similar to the prestressed concrete slab described above.
Another method for achieving compaction and stabilization of the building-support fill is called surcharge preloading. This procedure is carried out by loading the building-support spoil with soil or mine-spoil material. The weight exerted by this mass (typically more than the planned building) will accelerate consolidation of underlying spoil. Settlement plates are placed on the spoil surface prior to fill placement; these are horizontal metal plates attached to vertical riser pipes that extend upward through the surface material, allowing the rate of spoil settlement to be monitored with surveying instruments. When the downward movement of the settlement plates slows to an acceptable rate, the surcharge load is removed and the building site is prepared for construction.
On sites that are more than 2 years old, a less costly alternative to surcharge preloading may be available. Removal of the upper 10 to 20 feet of spoil would expose materials that have been compacted by overlying spoils over time. In some cases, this would be less costly than applying surcharge material, because the spoil that needs to be moved must be handled only once. Of course, this procedure will lower the ground surface, requiring a disposal location for the excavated spoils.
Case Study: Fill Stabilization of the Red Onion Maximum-Security Prison Site
Red Onion Prison was constructed on a reclaimed mine site at the border of Wise and Dickenson counties. The following text describes procedures required to stabilize the site as needed to support the prison.
The 16-acre site is a former surface mine that was reclaimed in the late 1980s. Controlled spoil-placement and compaction procedures were not employed during reclamation because the mining company did not expect the site to be used for building construction. The result was a relatively flat landform that was perfectly stable from an environmental standpoint, but it lacked the high level of structural stability required to support the prison’s precast masonry building units. Depths of spoil under the proposed building location ranged from 30 to 50 feet. A site investigation and geotechnical engineering study conducted by Schnabel Engineering Associates in 1994 determined that the site’s subsurface provided insufficient support to allow the prison to be constructed effectively.
In 1994, the Virginia General Assembly allocated funds to construct the prison on a portion of 300 acres of land donated to the state by Pittston Coal Company. The funding included the amount needed to stabilize the site to support the prison, based on an estimate prepared by Schnabel. Stabilization consisted of a combination of dynamic compaction and surcharge procedures. Both procedures were applied because of the maximum-security prison project’s sensitivity. In most cases, either one of these two procedures would be adequate.
Dynamic Compaction
All building-support areas (approximately 8 to 9 acres) were treated with dynamic compaction using weights of 11 and 15 tons dropped from heights of 25 to 70 feet. The dynamic compaction procedure was applied to the building site in four passes. Ground conditions determined the size and shape of the weight used at each location. The first two passes were conducted as high-energy passes with 15-ton weights on offsetting 15-foot grids within the building footprint and in all areas located 20 feet or less from the footprint. The weight was dropped eight times from a height of 70 feet at each location. The third pass was also high energy and further compacted mine spoil beneath the building’s support footings, with three drops per location from a height of 70 feet. At large column-footing locations (5 square feet or larger), four points were applied per column, while locations of smaller columns were treated at a single location per column. The final pass consisted of a low-energy application covering the entire building footprint using the lighter-weight 25-foot drop and two drops per location.
Several different 15-ton weights were used in the high-energy compaction procedures. Where the ground was relatively soft (where uncompacted, soil-like materials were present at the surface), a weight exerting 900 pounds per square foot (psf) of contact pressure was used; this weight had a 32-square-foot footprint area. Two 1,500 psf (20 square foot) 15-ton weights were used in areas of rocky or compacted fill.
Surcharge
A 15-foot depth of soil and rock materials was applied as surcharge to areas of the site that would support buildings, and 10 feet of surcharge was applied to future locations of roadways, parking areas, and similar facilities (see figures 5 and 6). Surcharge was applied to an area of approximately 10 acres. This is slightly larger than the area that received dynamic compaction, which did not include road and yard facilities. The surcharge was designed to exert a pressure of approximately two times that expected of the completed building; about 250,000 cubic yards of surcharge material were required. The length of time required of the surcharge for stabilization to occur was determined by placing settlement plates with extension rods in the original fill prior to surcharging; these plates were firmly based in the original fill and extended vertically above the surcharge fill. Movement of the underlying fill was monitored with reference to the protruding stanchions. Most areas of the original fill surface moved downward by 1 to 2 inches as a result of the surcharge operation. When the design settlement had been achieved (an average of three months after original placement), the surcharge was removed.


On some portions of the site, it was necessary to remove more than 15 feet of existing spoil prior to construction so as to reach final grades. No surcharge was applied in these areas.
Costs
The cost to prepare the 16-acre prison site for construction was $8 million to $9 million; most of the activity occurred during 1996. About $4 million of this total covered costs required for the dynamic compaction, surcharge, and associated procedures. Of these costs, dynamic compaction was responsible for approximately $1 million, while surcharge was responsible for approximately $3 million, predominantly-earth moving costs. The remaining site-preparation costs consisted of site grading, erosion and sediment control, and roadway construction.
Conclusion and Summary
Land-use constraints restrict economic development throughout the Virginia coal-mining region and in adjacent Appalachian areas. Although widely discussed, the potential of using surface coal-mining operations to relieve this constraint by preparing land suitable for improved use has not been realized. Experience has shown that reclaimed land suitable for building sites will often require more than just a flat surface. In order to minimize postmining settlement within a few years after mining, it is essential that appropriate spoil-placement procedures be utilized in constructing the building-support fill during reclamation.
Lands reclaimed using conventional practices will often remain subject to rates of postmining settlement that are considered unacceptable by most land developers for many building types – even years after mining. In time, settlement of these lands will essentially cease, but in most cases, many years will be required. It is possible to employ procedures that will accelerate stabilization of settlement-prone mined land. However, site-stabilization procedures require a considerable expense.
This publication contains only general background information and guidelines. Both site-stabilization and spoil-placement procedures to minimize postconstruction settlement should be designed in consultation with a professional engineer.
Acknowledgments
Thanks to the following individuals for their help with this publication: Bob Tuck, Roger Jones, Ken Roddenberry, Gary Dingus, Deborah Aylor, Brown, and Bob Krebs.
References
Krebs, R. D. 1987. Residential Foundations for Reclaimed Land. Department of Civil Engineering, Virginia Tech.
Krebs, R. D., and C. E. Zipper. 2009. Foundations for Housing on Reclaimed Mined Lands. Virginia Cooperative Extension publication 460-115. http://pubs.ext.vt.edu/460-115.
Virginia Cooperative Extension materials are available for public use, reprint, or citation without further permission, provided the use includes credit to the author and to Virginia Cooperative Extension, Virginia Tech, and Virginia State University.
Virginia Cooperative Extension is a partnership of Virginia Tech, Virginia State University, the U.S. Department of Agriculture (USDA), and local governments, and is an equal opportunity employer. For the full non-discrimination statement, please visit ext.vt.edu/accessibility.
Publication Date
July 28, 2023